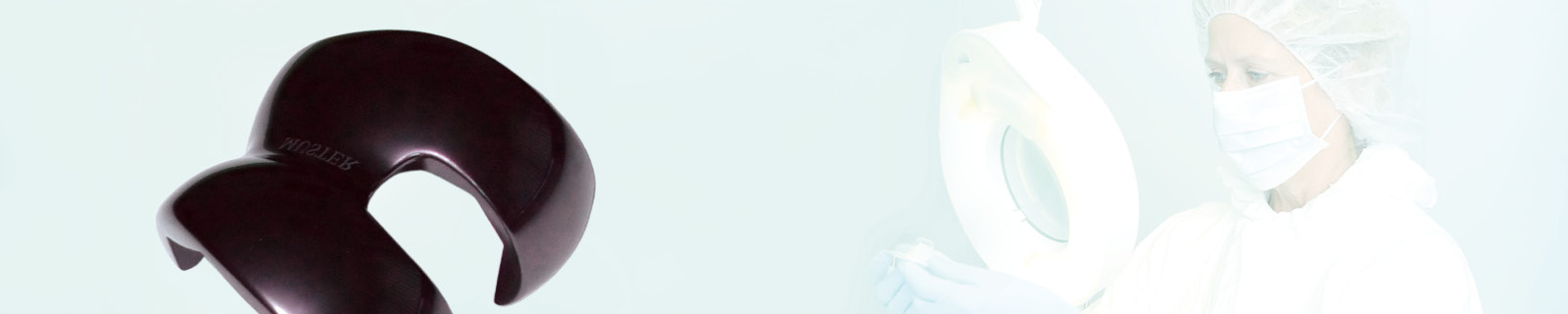
Titanium Aluminium Nitride (TiAlN)
Properties
- Coating thickness: 0.5-6 µm
- Adhesion strength: at least HF 1 (DIN EN ISO 26443)
- Coating hardness: ~2,700 HV
- Increased wear resistance
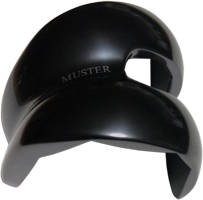
DOT GmbH
Charles-Darwin-Ring 1a
18059 Rostock l Germany
Phone: +49 381- 4 03 35-0